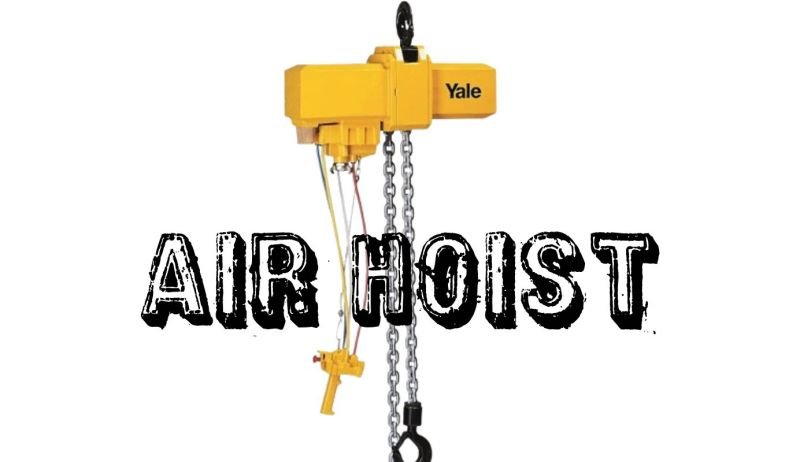
What is an air hoist?
Air hoist, also known as pneumatic hoist, is a lifting equipment using compressed air as the power source. These cranes are typically used in industrial environments where electricity may be inappropriate or unavailable or where electrical hazards exist, such as where flammable gases or combustible materials are present.
Air hoists usually consist of a motor, a gearbox and a pneumatic lifting mechanism. Compressed air is supplied to the hoist, which then drives the motor to lift and lower the load. Air hoists vary in design, but they are generally known for their durability, reliability, and ability to handle heavy loads.
Due to their use of compressed air as the power source, pneumatic hoists are often the first choice in industries such as mining, oil and gas, shipbuilding and manufacturing, where robustness and safety are paramount. They are also preferred in environments where electrical sparks may ignite flammable materials, as air hoists do not generate sparks during operation.
Overall, air chain hoists are valued for their robustness, suitability for hazardous environments, and ability to lift heavy loads safely and efficiently.
What is the purpose of a hoist?
The primary purpose of a hoist is to lift and lower heavy objects safely and efficiently. Hoists are an essential tool in various industries including construction, manufacturing, warehousing and logistics. They provide a mechanical advantage by using pulleys, chains, or ropes to increase the force exerted by the operator, allowing them to lift objects that are too heavy to move manually.
The key purposes of hoists include:
Material Handling: Cranes are used to lift materials and equipment vertically to facilitate tasks such as loading and unloading trucks, moving heavy machinery, and positioning components during assembly.
Load positioning: Cranes provide precise control over the positioning of loads, allowing operators to place them exactly where they are needed, whether on a construction site, manufacturing plant or warehouse.
Safety: Cranes help minimize the risk of injury when manually lifting and moving heavy objects. By mechanizing the lifting process, hoists reduce the strain on workers’ bodies and decrease the likelihood of accidents caused by dropped or mishandled loads.
Efficiency: Hoists improve efficiency by speeding up material handling processes, reducing downtime, and increasing productivity. They enable workers to move heavy loads with minimal effort and in less time compared to manual methods.
Versatility: Hoists come in various types and configurations, allowing them to be adapted to different environments and applications. Whether it’s a small workshop or a large industrial facility, there’s a hoist available to suit specific needs.
In essence, hoists play a crucial role in streamlining operations, enhancing safety, and improving productivity across a wide range of industries. They are indispensable tools for lifting and moving heavy loads efficiently and safely.
Which is better electric hoist or air hoist?
Whether an electric hoist or a pneumatic hoist is better depends on a variety of factors, including the specific needs of your application, the operating environment and your budget constraints. Let’s compare the two:
Advantages:
Ease of use: Electric hoists are generally easier to install and operate, and only require a power source.
Precise control: They provide precise control over raising and lowering operations, making them suitable for delicate tasks.
Smooth operation: Electric hoists provide smooth and consistent lifting, which is beneficial for certain applications.
Indoor use: They are ideal for indoor applications where power is sufficient.
Considerations:
Environmental limitations: Electric hoists may not be suitable for use in environments where there is exposure to flammable gases or combustible materials due to the risk of sparks.
Purchase Cost: Compared to a pneumatic hoist, the purchase cost can be higher, especially if additional safety features are required.
Air Hoist:
Advantages:
Durability: Air hoists are known for their robustness and ability to withstand harsh environments, making them suitable for outdoor and rugged applications.
Explosion-proof: They inherently lack electrical components, reducing the risk of sparks, and making them suitable for hazardous areas.
Heavy Load Capacity: Air hoists are capable of handling heavier loads compared to electric hoists of similar size.
Lower Operating Costs: In some cases, air chain hoists may have lower operating costs, especially if compressed air is readily available.
Considerations:
Need for Compressed Air: Air hoists require access to a compressed air supply, which may not be available in all settings.
Installation and Maintenance: pneumatic hoists may require additional installation and maintenance considerations compared to electric hoists.
Control: They may not offer the same level of precise control as electric hoists, which can be a consideration for certain applications.
Ultimately, the choice between an electric hoist and an air hoist depends on your specific needs and priorities. If you prioritize precise control and ease of use, an electric hoist may be the better option. However, if durability, explosion-proof capabilities, and heavy load capacity are critical factors, a pneumatic hoists could be more suitable. Consulting with industry experts and considering the requirements of your application will help you make an informed decision.
What are the two main types of hoist?
Air hoists and air balancers are both pneumatic lifting equipment used in industrial settings, but they serve different purposes and work in different ways. Here’s a breakdown of the main differences between the two:
Function:
Air chain hoist: Air work hoist is mainly used to lift and lower heavy objects vertically. It works similarly to other types of lifting equipment, using compressed air as a power source to lift objects.
Air Balancer: Air balancers, on the other hand, are designed to aid in load handling by providing ergonomic support to workers during material handling tasks. It is often used for tasks such as assembly line work that require workers to maneuver loads horizontally and vertically with minimal effort.
Mechanism:
Air hoist: Air hoists typically use a motor-driven mechanism and pulleys, chains, or ropes to lift and lower loads. They allow precise control of the lifting process and are capable of handling heavy loads.
Air Balancer: The air balancer functions differently. It is composed of a pneumatic lifting mechanism that uses compressed air to make the load float; this creates a situation where minimal force is required from the operator, thus allowing the load to be easily moved up and down. The principle behind air balancers is to ensure that there is constant tension on the load, meaning that it feels weightless in the hands of the operator.
Application:
Air Hoist: Air hoists find great use cases in lifting heavy loads vertically due to tasks such as manufacturing, construction or mining demand. They are appropriate for jobs like lifting machinery and positioning components or materials since they provide easy access at any height with little effort involved by operators.
Air Balancer: Air balancers are generally utilized in assembly line works where workers have to control loads in various directions and with accuracy, they serve the purpose very well. They find their applications commonly in jobs involving lifting and placing components during assembly— thus reducing fatigue among workers which also further contributes to increasing efficiency in the work process.
Weight capacity:
Air Hoist: The range of capacities for air hoists is broad and starts from a few hundred pounds to many tons. This allows them to be efficient in carrying massive loads.
Air Balancer: In comparison with air hoists, air balancers are meant for lighter loads even though they are still capable of lifting considerable weights. Their main purpose, however, is not centered on handling very heavy objects but rather on ensuring ergonomic assistance.
To wrap it up, air hoists and air balancers share the use of compressed air for lifting, but their functionality and application are not similar. Air hoists are special-purpose lifting equipment mainly used to lift loads vertically; conversely, air balancers are engineering devices that help workers handle loads easily with little effort, especially in environments like assembly lines.
Conclusion
In conclusion, air hoists represent a robust and reliable solution for lifting heavy loads in industrial environments. Their utilization of compressed air as a power source ensures safety in settings where electrical hazards are a concern, making them invaluable tools in industries such as mining, oil and gas, shipbuilding, and manufacturing. With their durability, explosion-proof design, and ability to handle heavy loads efficiently, air hoists continue to play a vital role in improving workplace safety, productivity, and overall efficiency. As industries evolve and safety standards continue to advance, air hoists stand as a testament to innovation and engineering excellence in the realm of material handling equipment.