VISÃO GERAL E USO:
O QJH guincho pneumático é alimentado por um motor pneumático tipo pistão AMH, projetado para operação de tambor único. Usado principalmente em minas de metal, minas de carvão, engenharia de construção e campos de petróleo para transportar e levantar objetos pesados.
Seu tamanho compacto, construção leve, velocidade ajustável, facilidade de manuseio e instalação rápida o tornam particularmente adequado para operações subterrâneas em ambientes de mineração. Ele se destaca em tarefas como despacho em estações de carga, transporte de caminhões de mina e elevação e tração de ferramentas e instrumentos pesados em becos subterrâneos estreitos.
Com seu design robusto e funcionalidade versátil, o guincho pneumático QJH é uma solução confiável para diversas aplicações industriais, oferecendo eficiência e conveniência em ambientes de trabalho exigentes.
ESTRUTURA E PRINCÍPIO DE FUNCIONAMENTO:
A estrutura e o princípio de funcionamento do guincho pneumático QJH são fundamentais para sua eficiência e funcionalidade. Alimentado por ar comprimido, este guincho emprega um motor pneumático de pistão e um mecanismo de redução com pares de transmissão de engrenagens interna e externa. Esses componentes trabalham em conjunto para acionar a operação do tambor, facilitando o processo de guincho de forma eficaz. As principais estruturas do guincho compreendem motores pneumáticos, caixas de engrenagens, tambores e freios. Por meio deste design integrado, o guincho pode fornecer desempenho robusto em várias aplicações industriais, garantindo operações confiáveis de elevação e transporte.
FREIO DO GUINCHO:
Os sistemas de freios de guincho desempenham um papel crítico em garantir a segurança e o controle durante as operações de guincho. Aqui está uma visão geral dos diferentes tipos de freios de guincho:
Freio a tambor manual (padrão): Este tipo de freio é operado por uma alavanca que pode ser pressionada para engatar o freio ou puxada para cima para liberá-lo. Quando totalmente pressionada, a alavanca trava, impedindo que o tambor gire até que seja liberado. O ajuste adequado é essencial para manter a carga necessária.
Freio de pé (padrão): Composto por correia de freio, correia de aço, pedal e outros componentes, o freio de pé funciona de forma semelhante a um freio de cilindro. No entanto, ele difere porque só é operacional quando o guincho está em uso. Quando o pedal é pressionado, a correia de freio e o cubo do freio engatam, aumentando a força de frenagem com a pressão do pedal. É útil para pausas curtas durante operações de elevação ou frenagem de emergência quando o guincho não é controlado ativamente.
Cilindro de freio a tambor (função opcional): Composto por correia de freio, correia de aço e um cilindro autocentrante, este freio oferece força de frenagem ajustável. Apertar a porca ajusta o aperto entre a correia de freio e o cubo do freio, permitindo níveis variados de força de frenagem. Quando o guincho opera, o gás comprimido entra no cilindro, encolhendo a haste do pistão para liberar o cubo do freio, permitindo a rotação do tambor. No caso de baixa pressão de ar ou corte de gás, uma mola de autorretorno aperta a correia de freio para completar a frenagem.
Freio a disco automático (função opcional): Esses freios utilizam mecanismos de frenagem por mola e liberação de ar. Um pistão acionado por ar e carregado por mola desengata automaticamente o freio quando o motor funciona, e os freios são acionados quando o acelerador retorna à posição neutra. A liberação do freio ocorre superando a pressão da mola e movendo o pistão por meio da pressão do ar na carcaça do freio.
É importante observar que a exposição prolongada a ambientes corrosivos pode fazer com que as lonas de freio de cinta grudem no tambor de freio. Durante períodos de inatividade, é recomendado deixar o freio de correia na posição liberada para evitar tal aderência.
Cada tipo de freio de guincho oferece vantagens distintas e é adequado para aplicações específicas. A seleção e manutenção adequadas do sistema de freio são cruciais para garantir segurança, controle e eficiência durante as operações do guincho.
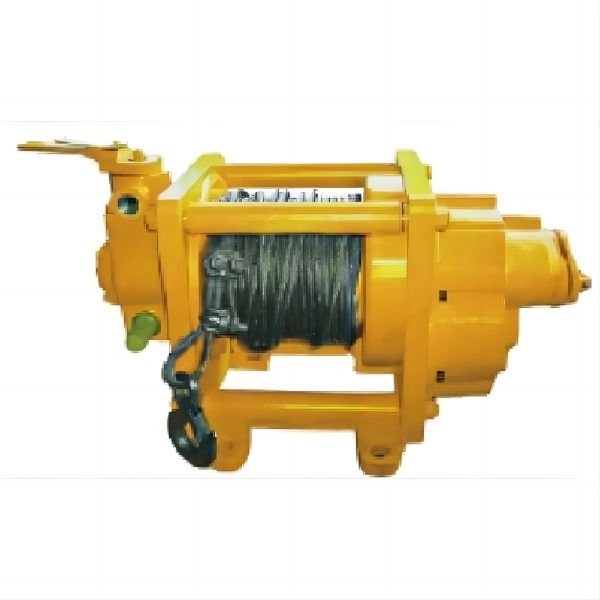
Guincho pneumático 0,1T-8T
Os guinchos pneumáticos da KRC fornecem elevação segura e confiável de capacidades de 0,1T a 8T para aplicações industriais. Alimentados por ar comprimido e controlados manualmente ou remotamente, esses guinchos apresentam frenagem automática, operação flexível, designs leves e acabamentos resistentes à corrosão.
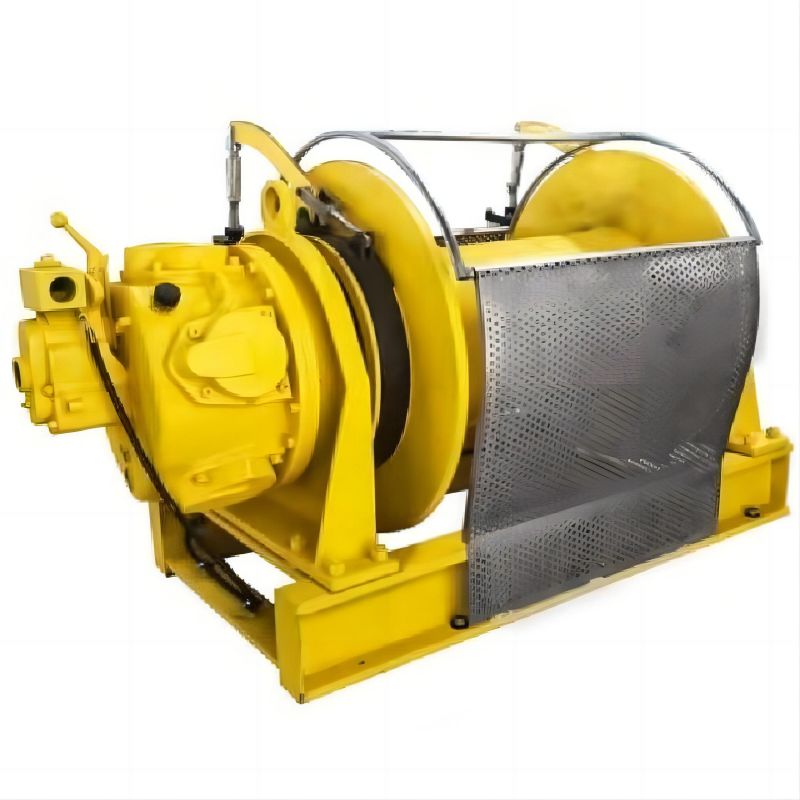
Guinchos pneumáticos 10T-15T
Uma série de guinchos pneumáticos para serviço pesado com capacidade de 10 a 15 toneladas, adotam acionamento por motor pneumático de pistão, modelos de controle manual/remoto, equipados com freio de mão + freio a ar para elevação segura.
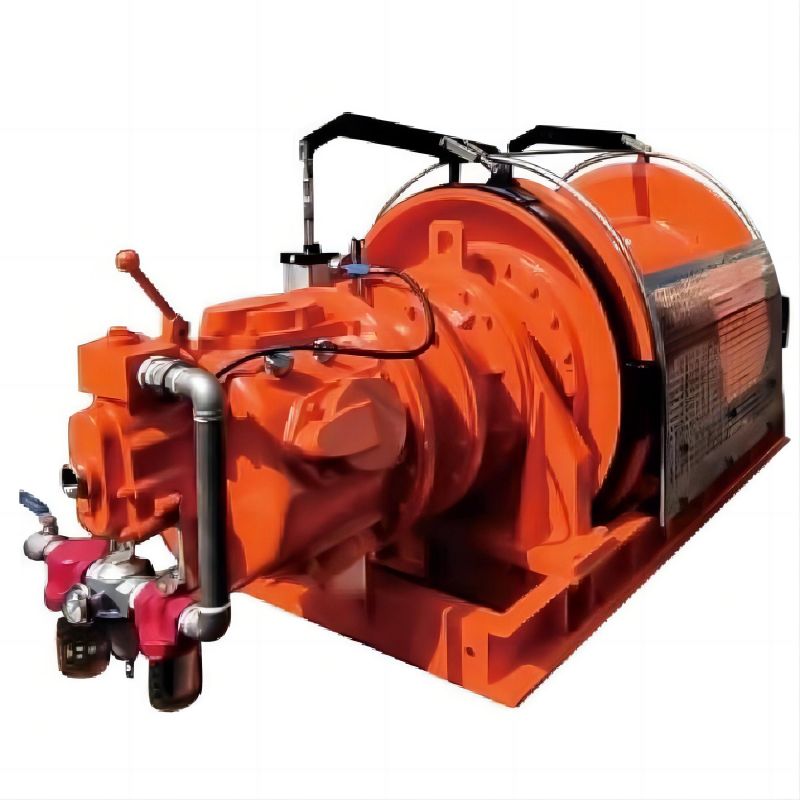
Guincho pneumático 25T
Guincho de alto desempenho de 25 toneladas movido a ar comprimido, com controle manual (remoto opcional), acionamento por motor pneumático tipo pistão, torque de redução planetária, freio a disco automático e freio a ar duplo para força de frenagem, estabilidade e segurança excepcionais. Capa protetora de aço inoxidável 304 com tinta anticorrosiva marítima garante durabilidade.
LUBRIFICAÇÃO:
Para garantir que o guincho pneumático continue a operar suavemente, todos os pontos de lubrificação devem ser atendidos com o lubrificante correto em intervalos apropriados de acordo com as especificações de cada componente. Use apenas os lubrificantes recomendados, pois outros lubrificantes podem afetar o desempenho do produto.
Use sempre o tipo de óleo recomendado para evitar danos ao guincho e/ou seus componentes associados. O uso de óleo inadequado pode resultar em altas temperaturas, eficiência reduzida e danos potenciais às peças lubrificadas. Consulte a tabela de lubrificantes recomendados. Intervalo de lubrificação
Recomenda-se realizar a primeira troca de óleo após aproximadamente 50 horas de operação inicial. Posteriormente, descarregue e substitua o óleo de acordo com os intervalos especificados para cada componente. Verifique o consumo de óleo do lubrificador da linha de ar diariamente.
Sempre inspecione o óleo drenado para sinais de danos internos ou contaminação (lascas de metal, sujeira, água, etc.). Verifique o nível de óleo do motor e investigue e corrija quaisquer sinais de danos antes de retomar a operação do guincho. Verifique a caixa de engrenagens e o óleo do freio a disco.
Deixe o óleo assentar antes de completar após a operação do produto.
Colete lubrificantes em recipientes adequados e descarte-os de forma ambientalmente segura. Substitua o óleo do freio a disco.
Produtos pneumáticos usam óleo para evitar superaquecimento e proteger contra desgaste que poderia causar faíscas. Níveis adequados de óleo devem ser mantidos para garantir que o guincho continue a operar suavemente. Todos os pontos de lubrificação devem ser atendidos com o lubrificante correto em intervalos apropriados de acordo com as especificações de cada componente.
FORNECIMENTO DE AR:
Para garantir o desempenho ideal do motor, o suprimento de ar deve ser limpo, livre de umidade e lubrificado adequadamente. Desgaste e falha prematuros do motor geralmente resultam de matéria estranha, umidade ou lubrificação insuficiente. Utilizar filtros de ar, lubrificadores e separadores de umidade melhora o desempenho do produto e minimiza o tempo de inatividade não planejado.
A instalação de lubrificadores de linha de ar, filtros e reguladores perto da entrada de ar do motor é crucial. O lubrificador deve ser posicionado dentro de um raio de 3 metros do motor. Além disso, considere montar o kit de acessórios da linha de ar em uma placa de proteção do guincho, no lado do operador ou oposto, para acesso conveniente.
A manutenção adequada do sistema de suprimento de ar é vital para a operação eficiente de guinchos e outros equipamentos pneumáticos. Verificações e substituições regulares de filtros, lubrificadores e separadores de umidade são recomendadas para manter os padrões de desempenho e prolongar a vida útil do equipamento.
INSTALAÇÃO:
Durante a instalação do guincho, é crucial manuseá-lo com cuidado, especialmente ao movê-lo ou posicioná-lo. Os olhais de elevação são normalmente fornecidos para ajudar a carregar o guincho, mas se eles não forem adequados para sua instalação específica, tome cuidado especial para garantir o equilíbrio adequado durante o levantamento.
Certifique-se de que o guincho esteja instalado com o eixo do tambor na horizontal e a distância entre a tampa de ventilação do motor de ar e o centro vertical do topo não exceda 15 graus. Se você pretende instalar o guincho em uma posição invertida, gire o alojamento do motor adequadamente, posicionando a tampa de ventilação na parte superior.
A superfície de montagem do guincho deve ser plana e robusta o suficiente para suportar a carga nominal, juntamente com o peso do guincho e qualquer equipamento adicional. Resistência insuficiente da fundação pode levar à deformação ou torção da coluna do guincho e do trilho lateral, resultando em danos.
Ao prender o guincho, use parafusos de montagem de Classe 8 ou superior, juntamente com porcas autotravantes ou porcas com arruelas de travamento. Certifique-se de que o ângulo entre o conjunto de polias e o guincho não exceda 1-1/2 graus. Além disso, alinhe a roda guia com a linha central do tambor e evite soldá-la a qualquer parte do guincho.
A instalação adequada é essencial para a operação segura e eficiente do guincho, garantindo longevidade e desempenho ideal em vários ambientes industriais.