Choosing the right hoist is crucial for ensuring both safety and efficiency in lifting operations. Whether you’re lifting heavy materials in an industrial setting or handling delicate items in a controlled environment, there are several key factors to consider when specifying a hoist for your application. This guide will outline the most important aspects to help you make an informed decision.
1. Determine Required Capacity
The first step in selecting a hoist is determining the load capacity you need. For manual hoists, the rated capacity should at least match the weight of the heaviest load you plan to lift. However, when choosing electric or pneumatic hoists, you also need to consider the Mean Effective Load (MEL) and apply the MEL factor of 0.65.
For a more detailed analysis of hoist capacity requirements, refer to ASME HST-1, Performance Standard for Electric Chain Hoists. Always ensure the hoist’s capacity is aligned with both the load weight and the structural limitations of your overhead system (pad eye, monorail, or beam).
2. Selecting Suspension Type
Hoists can be suspended in various configurations, depending on your application needs. Common suspension types include:
- Fixed Suspension: The hoist remains stationary.
- Trolley-Mounted Hoist: This type allows for movement along a rail system.
Trolleys can be either rigid or articulating, and their movement can be plain (push type), hand-geared, or motor-driven. The choice between fixed or trolley-mounted suspension depends on your workspace layout and the degree of movement required.
For more information on selecting the right suspension type for your system, visit Yale Hoist Solutions.
3. Choosing Lift, Reach & Headroom
When specifying your hoist, it’s essential to evaluate Ascenseur, Reach, et Headroom, as these factors are interrelated.
- Ascenseur: This is the distance the load hook can travel from its fully lowered to fully raised position.
- Reach: The vertical distance between the hoist suspension point (such as the pad eye or trolley beam) and the lowest point of the hook.
- Headroom: The space between the suspension point and the fully raised hook saddle.
Understanding these dimensions is critical to ensuring that your hoist fits within your operational space. Tight headroom or reach limitations may require a custom hoist solution, which can be addressed by working with professionals at Grues KRC.
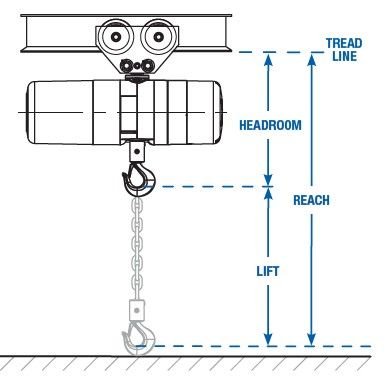
4. Power Supply Considerations
Different hoists require different power sources. Electric hoists typically operate on either single-phase (120 or 230 V) or three-phase (208, 230, 460, or 575 V) power. It’s vital to verify the power supply available in your facility before making a decision.
If you’re unsure which power supply is best suited for your hoist, Please contact our experts to help you choose.
5. Choosing the Right Control System
Hoists can be controlled manually, electrically, or pneumatically, depending on the application and operational requirements. Electric hoists are often equipped with various control types:

- Single-Speed or Two-Speed Contactors: These are the most basic control systems for electric hoists.
- Variable Frequency Drives (VFD): VFD systems adjust motor speed and torque by altering input frequency, allowing for more precise control over the hoist’s operation.
- Closed-Loop VFD Systems (Flux Vector Drives): These provide enhanced control, offering precise speed regulation and better load spotting, significantly improving safety and efficiency.
6. Lifting Speed Selection
Hoists are available with various lifting speeds, typically ranging from 3 FPM to 64 FPM. The appropriate lifting speed will depend on factors such as load weight, required speed of operation, and the total number of cycles to be completed in a specific time frame.
Higher lifting speeds may be required for fast-paced operations, while slower speeds can be ideal for more delicate or heavy lifting tasks. The torque requirement is directly tied to lifting speed, and the motor horsepower needs to be specified accordingly.
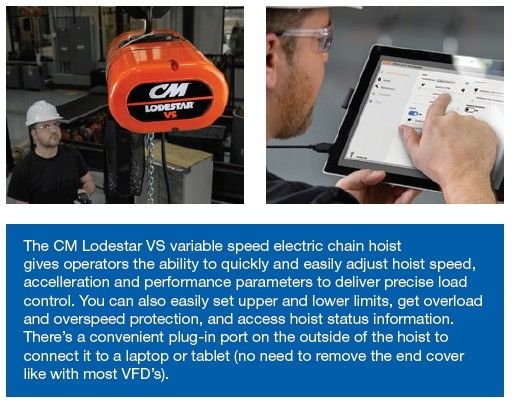
7. Selecting the Right Hoist for Special Environments
Standard hoists are designed for normal operating conditions, but if you are working in environments with extreme temperatures, outdoor areas, or corrosive atmospheres, you may need a hoist with special modifications. Hoists designed for environnements marins, clean rooms, ou wash-down areas are available, offering the necessary protection and features to ensure safe, reliable operation.
If you’re working in specialized environments, contact Grues KRC for tailored hoist solutions that meet your needs.
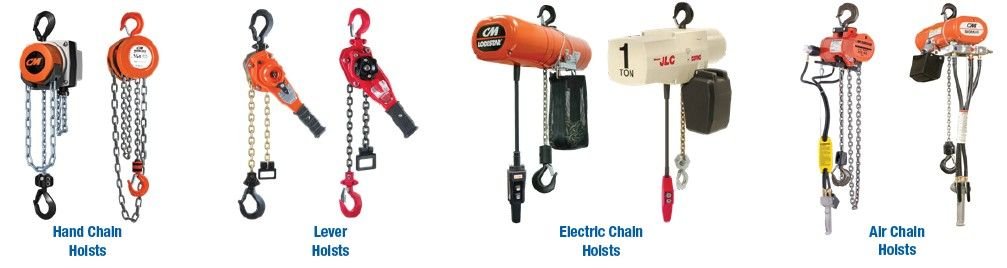
8. Dimensional Constraints and Space Planning
Before choosing a hoist, consider the available space for installation. Key dimensional considerations include:
- Headroom Clearance: Ensure that there is enough space above the hoist for safe operation.
- Side Clearance: Ensure there’s sufficient space along the monorail or crane beam.
- End Approach: This is the distance between the centerline of the lifting hook and the end of the beam or runway.
9.Determining Required Duty Class
Le American Society of Engineers (ASME) et le Hoist Manufacturer’s Institute (HMI) have developed and published standards for hoists, including duty classifications, to help users select the right equipment for their needs. These duty class ratings are determined by several factors, such as:
Hoist Duty | Applications | Uniformity Dist. Work Periods | Infrequent Work Periods | ||
---|---|---|---|---|---|
Max. On Time Min./Hr | Max. # of Starts/Hr | Max. On Time From Cold Start | Max. # of Starts | ||
H1 | Infrequent handling, loads frequency approach capacity and hoist idle for long periods between use. | 7.5 min. (12.5%) | 75 | 15 min. | 100 |
H2 | Loads and utilization randomly distributed; rated loads infrequently handled. Total running time not over 12.5% of the work period. | 7.5 min. (12.5%) | 75 | 15 min. | 100 |
H3 | Loads and utilization randomly distributed. Total running time not over 25% of work period. | 15 min. (25%) | 150 | 30 min. | 200 |
H4 | High volume handling of heavy loads, frequently near rated load. Total running time not over 50% of the work period. | 30 min. (50%) | 300 | 30 min. | 300 |
H5 | Equipment often cab operated. Duty cycles approaching continuous operation are frequently necessary. | 60 min. (100%) | 600 | N / A | N / A |
The table provided here, outlining the Hoist Duty Cycles, gives a clear understanding of the operational time ratings for various hoist duty cycles. The table helps users identify the most suitable duty class for their applications based on factors like work periods, load handling frequency, and maximum operational time.
10. Final Considerations and Expert Assistance
Selecting the right hoist involves balancing several factors, including capacity, suspension type, power supply, speed, and operational needs. At Grues KRC, we offer expert advice and a broad range of hoists tailored to your specific requirements. Our team can guide you through every step of the selection process, ensuring you choose the best hoist for your application.
For more personalized assistance with your hoist selection, contact our Application Experts.
By carefully considering the factors outlined in this guide, you can make an informed decision when selecting a hoist. Proper hoist selection not only enhances safety and efficiency but also maximizes the lifespan of the equipment. For further information on hoists and overhead lifting solutions, explore our comprehensive resources at Palans Yale.